Electrical connector
ASSAB Additive Manufacturing Solutions
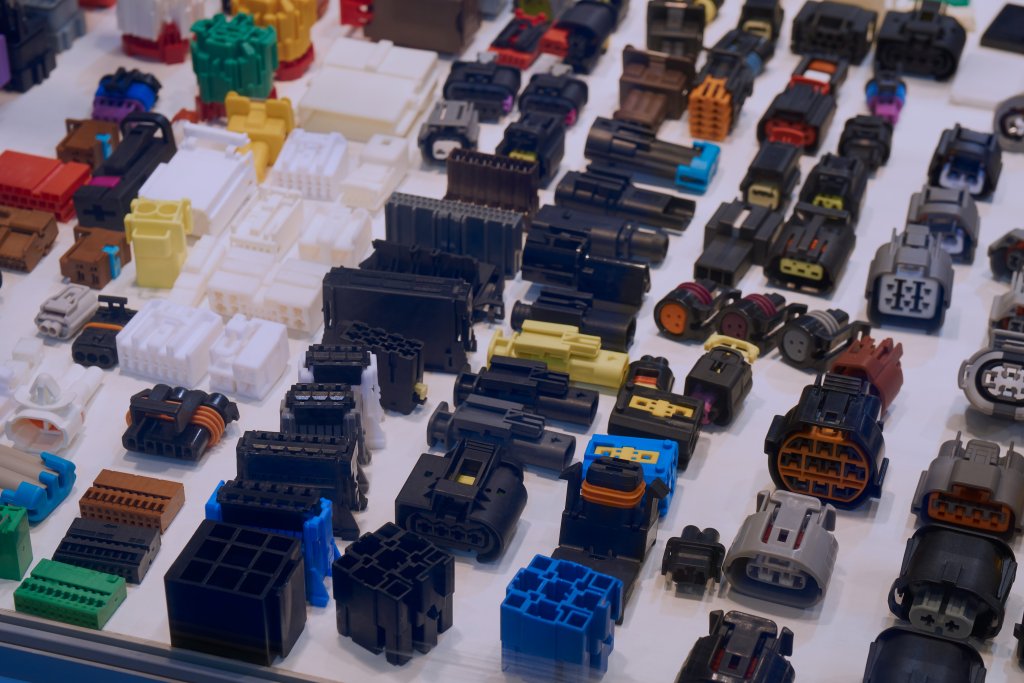
Electrical connectors in vehicles are crucial for establishing reliable and secure electrical connections, facilitating proper communication between various vehicle components. This enhances safety, performance, and overall functionality. Robust connectors are vital to withstand the harsh automotive environment, preventing electrical faults and ensuring the integrity of the vehicle’s electrical system. With modern vehicles increasingly reliant on electronic systems, sensors, and components for improved performance, safety, and connectivity, the demand for electrical connectors to interconnect these components is expected to grow. Thus, the need for more efficient methods of producing electrical connectors becomes increasingly important.
Beryllium copper (Be-Cu), known for its high thermal conductivity, has been a staple in electrical connector production. It efficiently dissipates heat during manufacturing, extending tool life by reducing thermal stress. However, conformal cooling channels have emerged as a worthy competitor, offering equivalent thermal conductivity, effectively matching Be-Cu’s performance in tool life extension.
Conformal cooling channels, when integrated into the mould design, can distribute cooling more evenly, reducing temperature differentials within the mould cavity. This uniform cooling minimises thermal expansion and contraction, ultimately enhancing tool life, similar to Be-Cu. The advantage of conformal cooling lies in its adaptability to complex mould shapes which can be challenging for traditional materials like Be-Cu.
Conformal Cooling in AM Inserts
The transition to additive manufacturing techniques has opened up new possibilities for design optimisation. In comparison to Be-Cu, the conformal cooling channels have shown remarkable advantages in specific areas:
1. Wear Resistance: Conformal cooling channels, often composed of advanced materials like tool steel or high-performance alloys, exhibit superior wear resistance. This characteristic makes them particularly well-suited for challenging manufacturing conditions, such as those involving glass fibre-reinforced composites. The resistance to abrasion and wear ensures a longer-lasting mould, reducing downtime for replacements.
2. Glass Fibre Reinforcement: Electrical connectors frequently involve the use of glass fibre-reinforced materials to enhance mechanical properties. Conformal cooling channels have proven to be more adaptable to these conditions, as they maintain their wear resistance and shape integrity even when subjected to the abrasive nature of glass fibres. In contrast, Be-Cu can experience wear and degradation more quickly under such conditions.
3. Heating/Cooling Efficiency: The design flexibility of conformal cooling channels allows for precise control over heating and cooling processes. By strategically positioning these channels, manufacturers can achieve faster and more efficient temperature regulation within the mould. This capability not only accelerates production cycles but also contributes to improved product quality by minimising thermal stresses and warpage.
Conformal cooling in AM Inserts can improve cooling efficiency against Be-Cu insert with conventional cooling channels
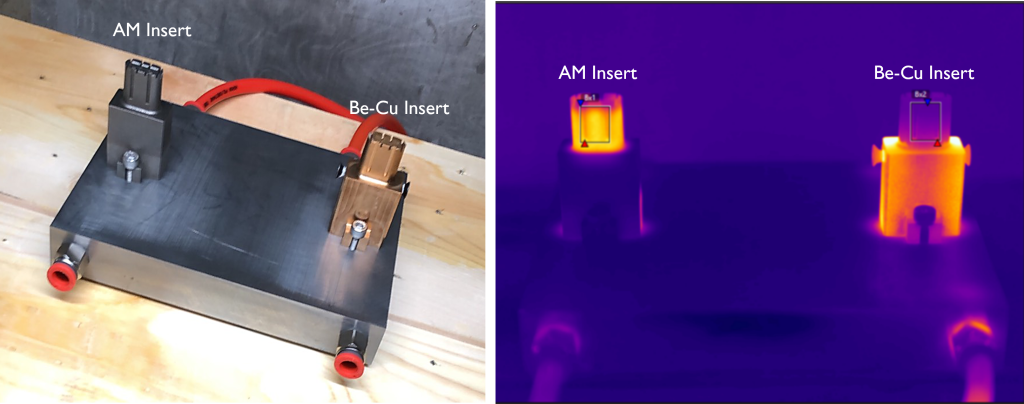
Reach out to us today for your Additive Manufacturing Solution.